Synthesis Bio-derived Infinitely Recyclable Polymers for Future Plastics
Cheap, light, and versatile plastics have become indispensable materials essential to our modern life and economy. However, over 90% of plastics produced are currently derived from finite fossil feedstocks, and less than 10% of plastic wastes were recycled in the US in 2014. The current recycling method is dominated by mechanical recycling into lower-in-value products without further recycling. Plastic disposal through land-filling and littering creates severe worldwide environmental consequences in marine, soil, and water systems. To address these concerns, the Li lab is working on the goal to manufacture 100% biomass-derived, highly recyclable, and biodegradable polymeric and copolymeric plastic that can be applied as packaging and grocery bags. In this project, the starting lactone building block is quantitatively recovered using thermal and chemical degradation methods in the presence of catalysts. The recovered monomer can be used again for producing lignin-grafted-polycaprolactone with similar properties. This technology allows production of chemically and infinitely recyclable plastic products. The goal of this project is to invent a modern cost-effective, bio-based polymer to (1) reduce the environmental impact of current plastic waste by improving recyclability and compostability, and (2) increase the economic value of forestry and agricultural feedstocks.
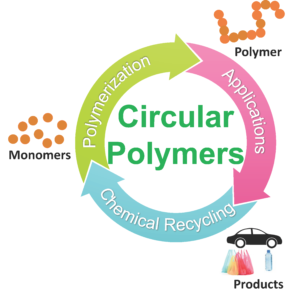
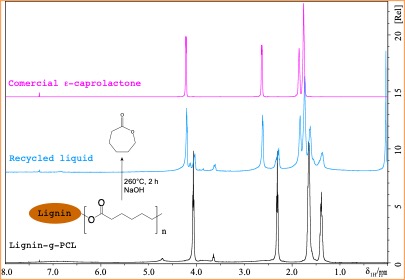
Converting Glucose to Value-added Glucarate Employing Novel Catalysts
Growing public awareness and concern about environmental pollution continues to drive the search for alternative resources to replace non-renewable fossil resources for energy and chemicals. Agro-crops and biomass continue to be promising feedstocks for biofuels and high-value chemicals for a wide range of industrial applications. The goal of this project in the Li lab is to develop novel technology to convert biomass-derived sugar into value-added chemicals. We will investigate the conversion of glucose into glucaric acid using efficient and recyclable oxidation catalysts. Glucaric acid is a promising chemical feedstock for the formation of biodegradable detergents, metal complexation agents, biodegradable polymers, films, adhesives, and plant fertilizers with wide applications. However, current industrial glucaric acid is primarily produced by chemical oxidation of glucose using non-selective nitric acid oxidation, with several issues including poor yields (~55%), upscaling challenges, and large waste generation. Therefore, we will manipulate the high selectivity of nitroxyl radicals on the oxidation of sugar to acidic analogs. By designing the feature of catalysts, we will attempt to improve the conversion yield and selectivity, reduce reaction pollution, and increase economic feasibility. This project will (1) increase the fundamental understanding of the chemical conversion of sugars to their sugar acids (i.e., aldaric acids); (2) help local and national growers discover and promote new and innovative market opportunities; and (3) advance the Bioeconomy and Carbon Circular Economy.
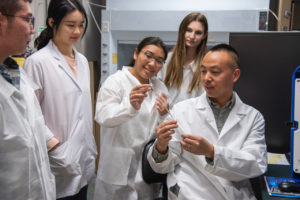
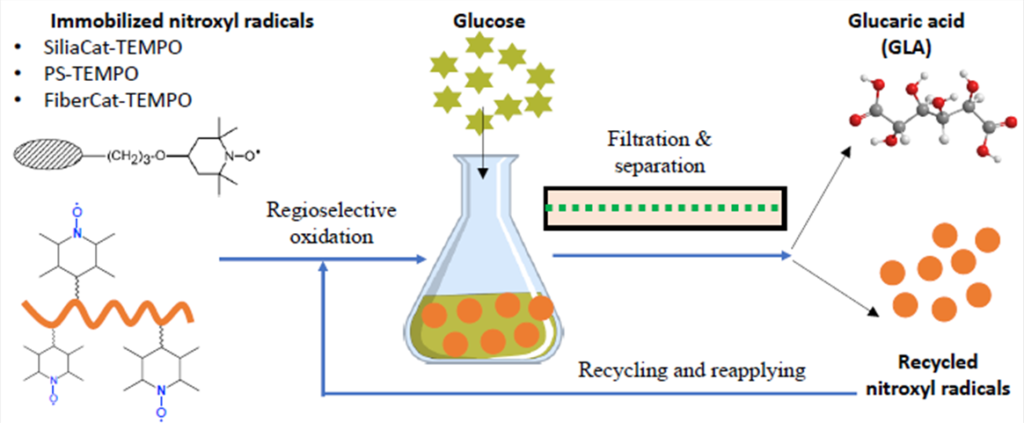
Ionic liquids-assisted fabrication of renewable films
Thin films (shown to the right, in the Labbé Lab) can be synthesized directly from woody and herbaceous biomass using ionic liquids-assisted wet solution casting technique. These films are 100% biobased and recyclable. They can be applied in multilayer packaging, energy storage and drug delivery systems
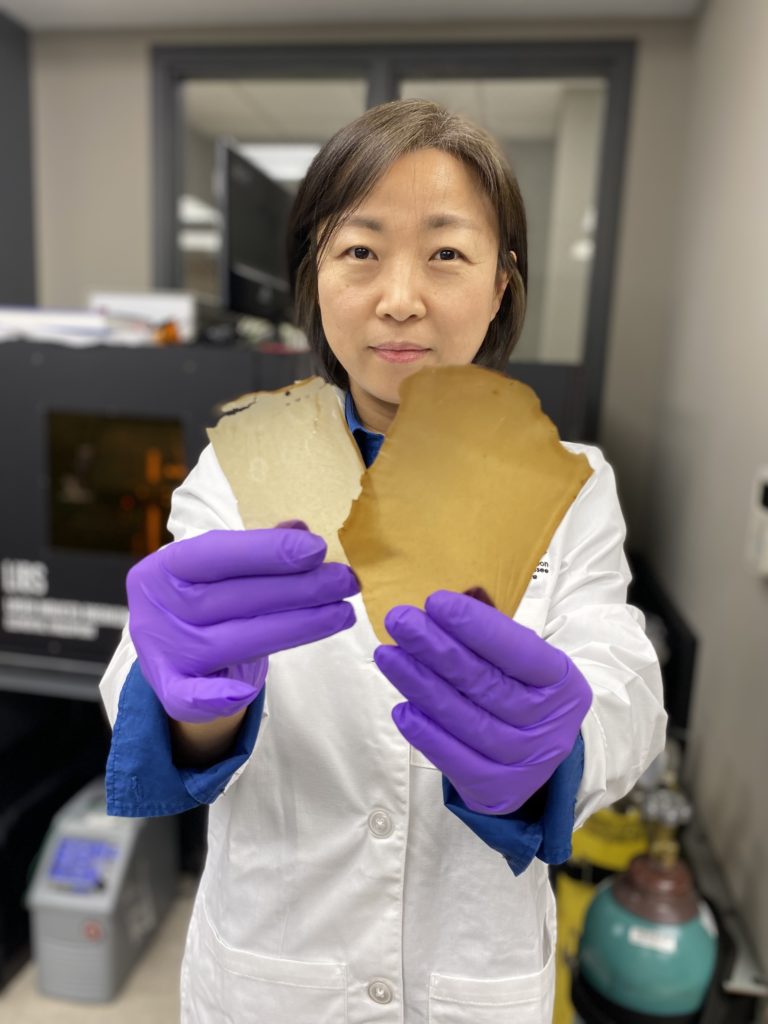
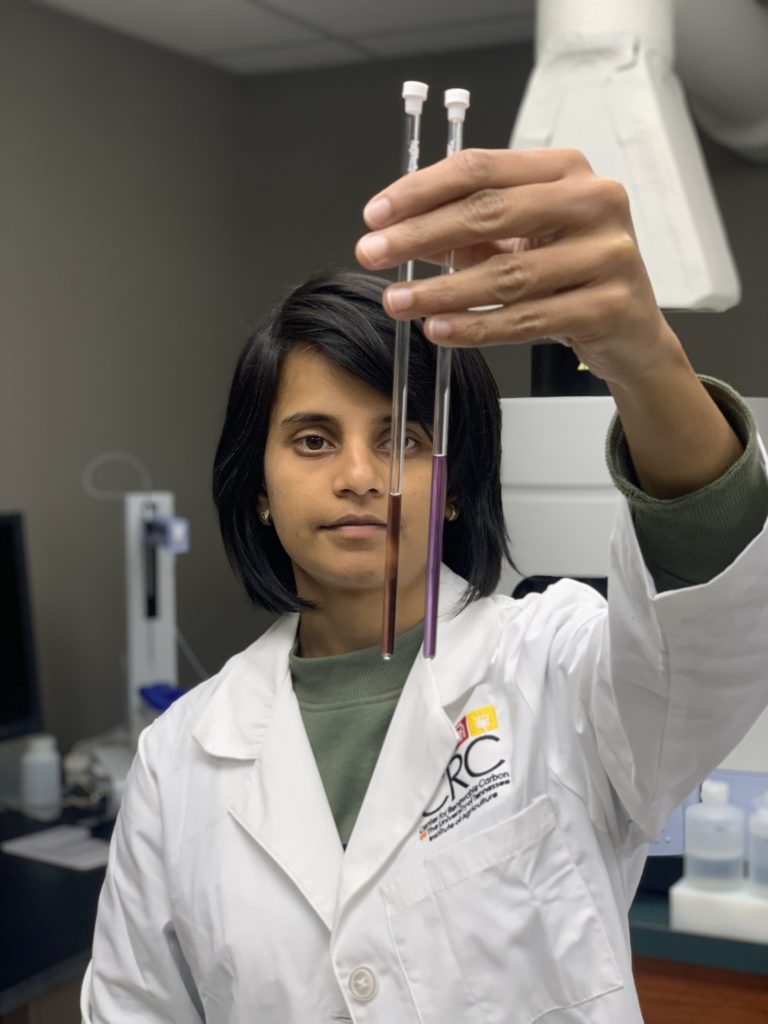
Fundamental structural elucidation of lignocellulosic feedstocks
Advanced characterization techniques like 2D-HSQC (Heteronuclear Single Quantum Coherence) nuclear magnetic resonance (NMR) spectroscopy are used to elucidate the nano- and microscopic structure of plant biomass (shown to the left, in the Labbé Lab). The research focuses specifically on how the fractionation technique affects the isolation of lignin from woody and herbaceous feedstocks, and how to develop functional materials from these feedstocks. The study results are applicable to the paper and pulp mills, a 34.3 billion dollar industry in the U.S., to sustainably valorize their lignin co-product stream.
Analytical services: Chemical and elemental composition of various biomass
The Labbé Lab routinely conducts biomass analytics services as a part of stakeholder support. In the photo to the right, plant biomass is analyzed for cellulose, hemicellulose, lignin, total extractives, and ash content, in addition to carbon, hydrogen and nitrogen content. The lab can also determine the sodium, potassium, calcium, sulfur, magnesium and lead content of various liquid and solid process samples. Research Associates in the Labbé lab are experts in modeling and predicting the chemical composition of lignocellulosic feedstocks based on their near infrared and Fourier transform infrared spectra.
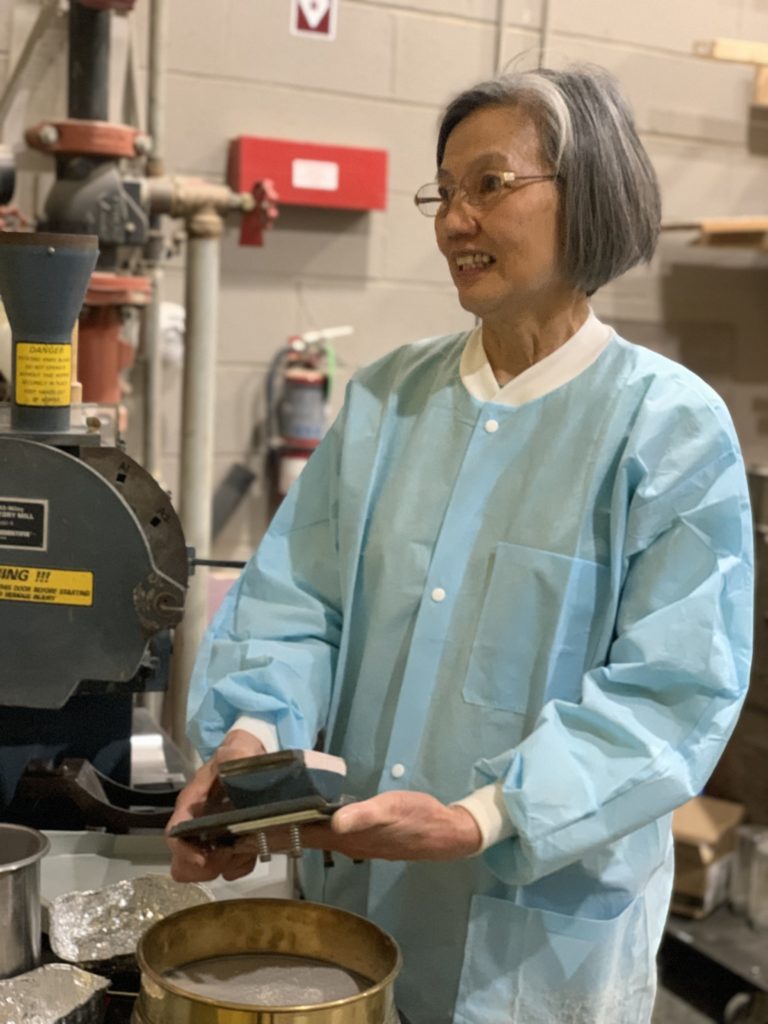
Exploring the Molecular Basis of the Prebiotic Potential of Biorefinery-relevant Feedstocks
This research explores the potential of sustainably available feedstocks as prebiotic substrates and the resulting changes in gene expression in microorganisms that adapt to these substrates. Probiotic bacterial viability will be examined on hemicellulosic oligosaccharides (HOS) isolated from feedstocks such as pine, switchgrass and hybrid poplar. Subsequently, bacteria grown on HOS will be analyzed using molecular-biology tools to identify the cellular mechanisms that confer adaptability to these different feedstocks. High-throughput RNA sequencing will be utilized to obtain a snapshot of the genome-wide changes that occur when a probiotic microorganism utilizes different sugars in the HOS. Overall, the data will help identify individual genes and molecular mechanisms involved in adaptation of probiotic microorganisms to carbon from different feedstocks.
Biomass Fractionation
Using lignocellulosic biomass as a feedstock to produce renewable fuels, chemicals and products implies dealing with heterogeneous materials that have evolved complex protective mechanisms to prevent physical, chemical and microbial degradation of the structural polysaccharides in their cell walls. More efficient organisms and systems that can rapidly breakdown the various polysaccharides present in biomass such as woody and herbaceous biomass are needed to make the cellulosic industry a reality.
Ionic Liquids
Ionic liquids show great promise as a host to biomass fractionation and utilization of each component in the production of fuels and value-added products.
Benefits to Ionic Liquids (ILs):
- Ability to solubilize biomass
- Low volatility
- Environmentally friendly
- Non-flammable
- “Designer solvent” for green chemistry
To fully exploit the benefits of ILs it is critical, BeST is developing compatible IL-enzymes systems in which the IL is able to effectively solubilize and activate the lignocellulosic biomass, and the cellulolytic enzymes possess high stability and activity.
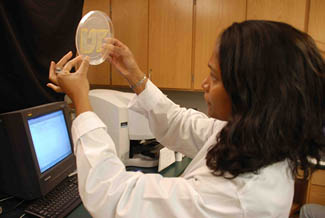
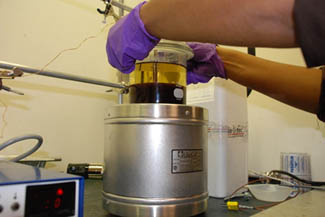
Iconic liquid-enzymes system to effectively fractionate biomass
Organic solvent fractionation of lignocellulosics
Biorefining, the process of converting renewable raw materials into biobased chemicals and fuels, bears many similarities to petrochemical refining. As received, both raw materials are difficult to use, as they are complex mixtures of different, simpler components. Crude oil contains multiple hydrocarbons spanning a wide range of molecular weights and boiling points, while lignocellulosic biomass is a mixture of cellulose, hemicellulose and lignin, along with much smaller amounts of extractable materials and inorganic salts. Thus, crucial to the utility of both feedstocks is an initial separation of the raw material into its simpler constituent parts, affording intermediates more versatile and easily used than the raw material itself. Treatment of biomass with organic solvents frequently meets this requirement. CRC research has developed a separation process using organic solvents that converts biomass into its individual cellulose, hemicellulose and lignin process streams. Each fraction can serve as a starting material for the production of biobased chemicals and fuels. The process being used at the CRC heats biomass with a mixture of methyl isobutyl ketone, ethanol, water and an acid promoter. This mixture selectively dissolves the lignin and hemicellulose leaving the cellulose as an undissolved material that can be washed, fiberized, and further purified. The dissolved solution of lignin and hemicellulose can be further separated into individual components. The process operates with high efficiency: greater than 95% of the components present in the starting feedstock is isolated after fractionation, and, for the lignin and cellulose fractions, in high purity, which is important for their eventual use as chemical building blocks. The cellulose fraction is generally 90-95% pure, and can be further purified using simple bleaching processes with environmentally friendly materials such as hydrogen peroxide. The lignin fraction is normally greater than 95% pure. Importantly, the process works well on multiple feedstocks, including switchgrass, poplar and southern yellow pine – all renewable feedstocks important to developing a biobased economy in the southeastern US.
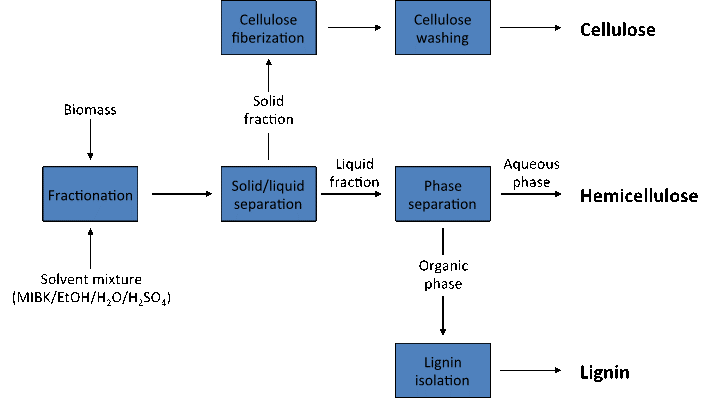
Catalyst design for lignin conversion
Lignin exists simultaneously as one of the most promising opportunities and greatest challenges for the lignocellulosic biorefinery. Access to this highly abundant renewable carbon source is growing, as pretreatment methodologies, such as the CRC organosolv process, affords lignin as a separate coproduct. Projections suggest that 2nd generation biorefineries may generate over 65 million tons of lignin or as much as 60% more than is needed to satisfy internal energy requirements. However, truly selective lignin transformations remain elusive, and as a result a promising source of renewable carbon generally remains relegated to use as a low-value fuel. Reducing lignin valorization to practice is still fraught with the well-recognized challenges of multiple feedstock sources, structures that change depending on both the source of the lignin and the methods used to isolate it from a lignocellulosic matrix, and a lack of simple, selective transformations tailored for its unique structure. CRC research addresses this problem by investigating new methodology for the selective, catalytic conversion of lignin into high value chemical products. We couple organic synthesis, catalyst design, mechanistic investigation and spectroscopy to develop catalyst systems tailored for the unique structures of lignin. Our focus areas include: Development of metal-Schiff base complexes for lignin oxidation – transformation of organosolv lignin into high value benzoquinones and low molecular weight aromatics